精益生产(lean production)是源自丰田生产方式的一种管理哲学。
丰田公司在探索新的生产模式过程中发现,小批量生产比大批量生产成本更低,原因有两个:
1、小批量生产不需要大量的库存,设备和人员
2、在装配前,只生产少量的零件,发现错误可以立即更正
根据这两个原因,丰田公司得出结论,应该将产品的库存时间控制在2个小时以内,即JIT(Just In Time,准时生产方式)和零库存的雏形,这就是精益理念的起源。
当下,国内生产企业的发展受到浪费问题的严重制约,资源投入与产出比例不相匹配,成本居高不下,且产品质量不能保证。
精益生产(lean production)就是解决浪费问题,提高企业生产效率,增强企业竞争力的一把钥匙。
精益生产的终极目标是实现“7个零”,与浪费问题直接对立:零转产工时浪费、零库存、零浪费、零不良、零故障、零停滞、零灾害。其核心思想就是最大限度地细化工作流程,消除浪费和一切非增值活动,以最小的投入获得最大的产出,向市场提供成本最低,质量最好的产品,以满足市场的需求。
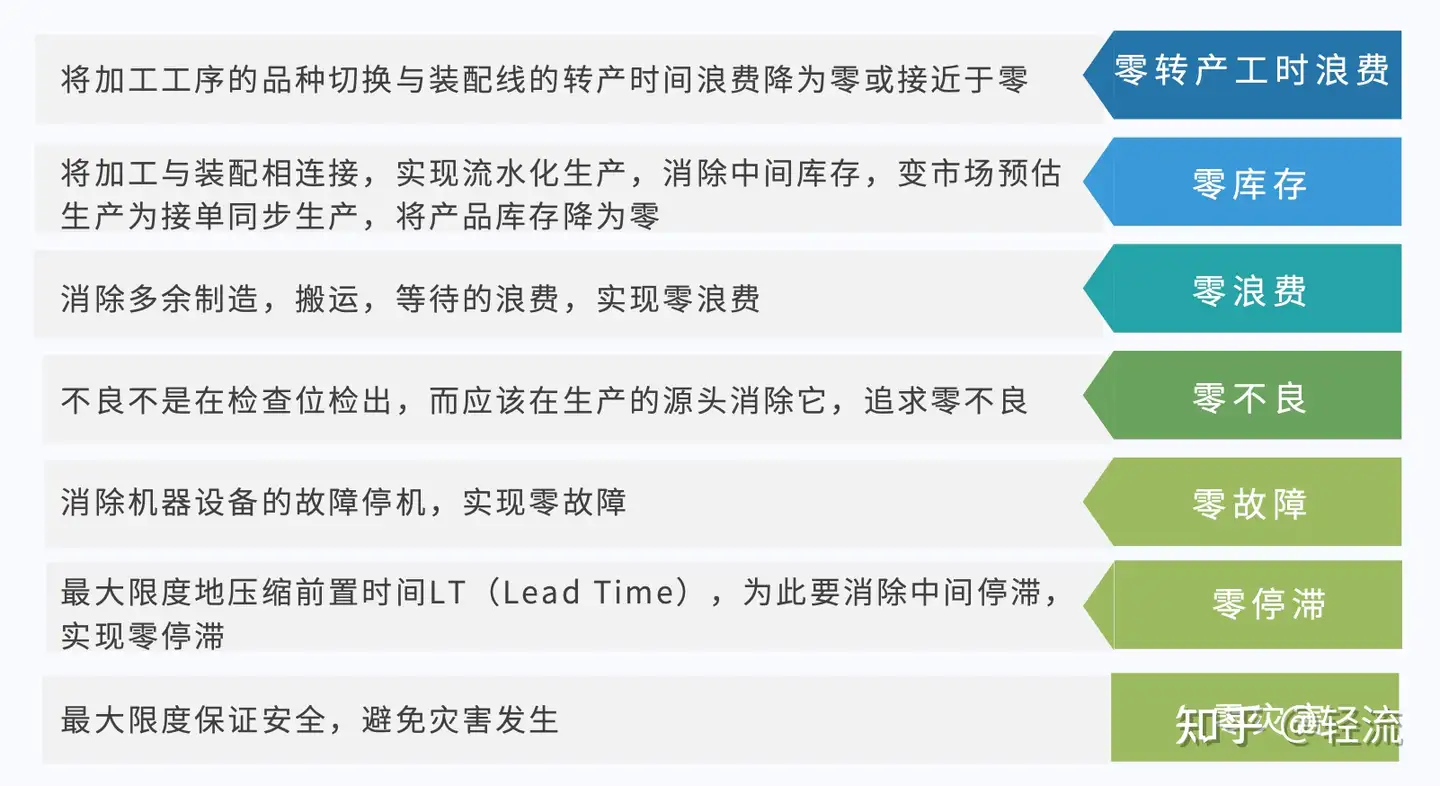
如何做到精益生产?
要有效落地精益生产管理,需要在两个层面作出努力。
第一层面在于企业内部。从管理者到一线员工都要明确精益生产的管理方式,各级管理者认可,精益化管理工作才能稳步推进,员工的参与程度直接决定精益生产能否取得实效,具体涉及六大关键因素:管理者认知、员工积极性、推行顺序、精准化切入点、树立标杆、营造氛围。
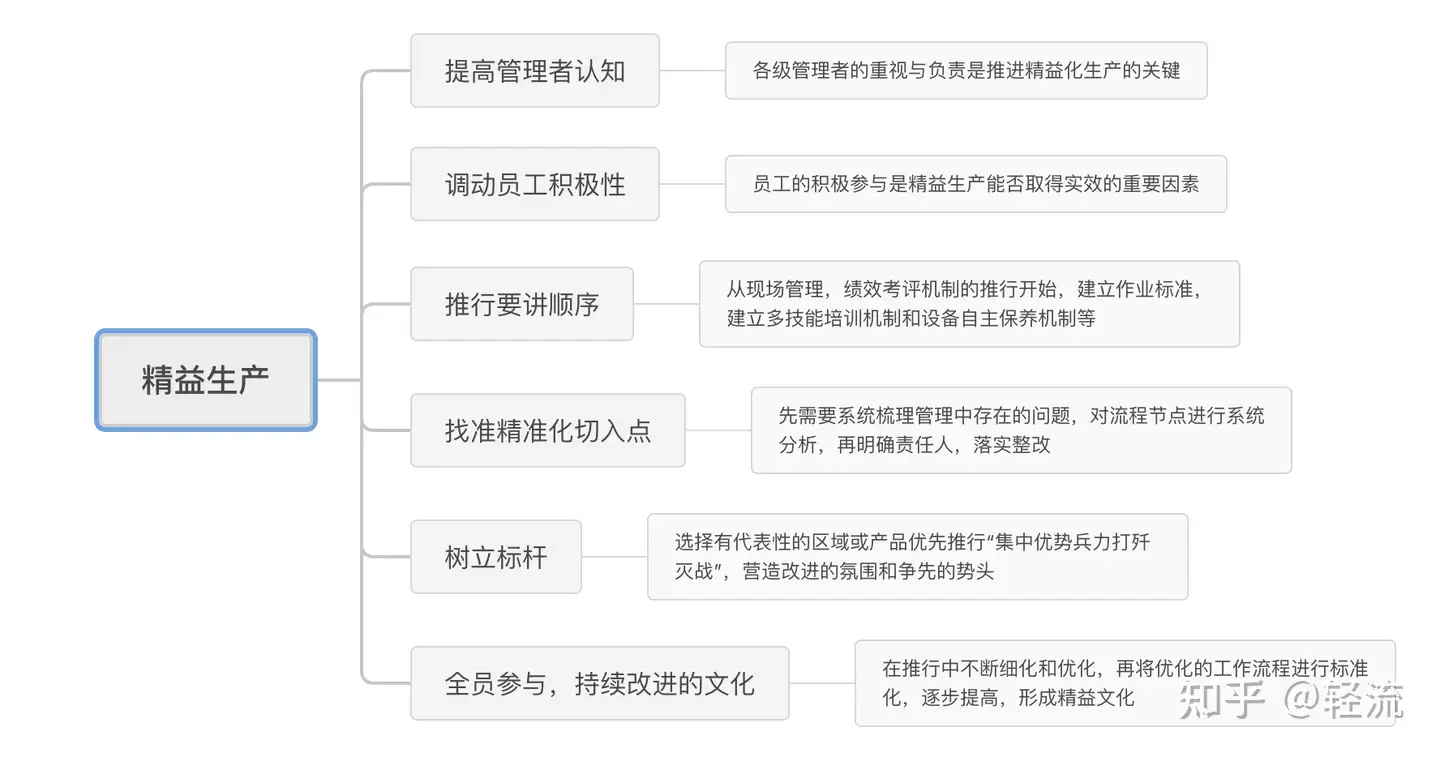
第二层面在于“工具”。欲善其事,必利其器。即使企业全体员工都明确精益生产的目标,若没有一个高效好用的工具仍会走弯路,难见实效。
轻流根据精益生产的六大板块:生产现场管理、品质管理、设备管理、采购与仓储管理、生产安全管理、成本控制管理上线了相应的解决方案模版,帮助制造业企业能够顺利实施精益生产。
1、CI(合理化建议)
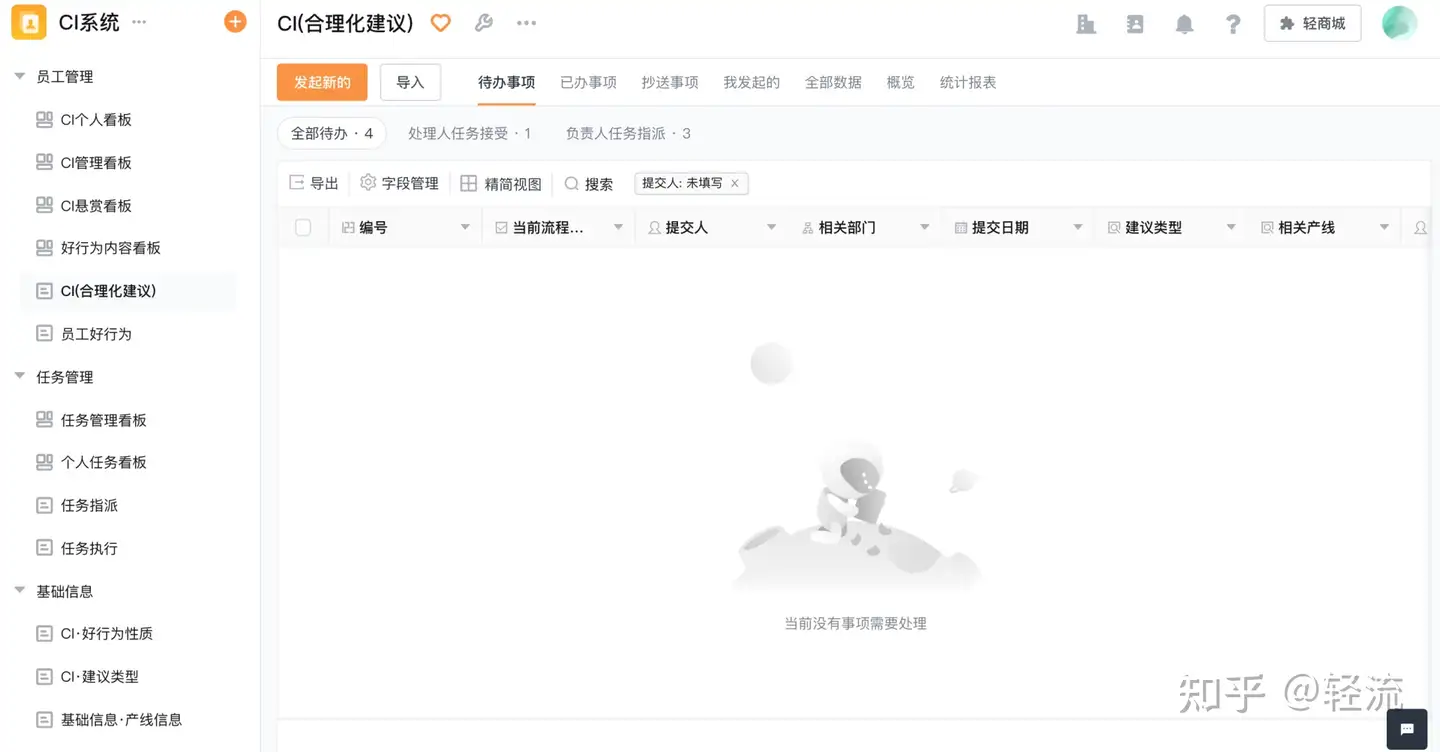
合理化建议从生产环境、工序流程、生产设备三个方面进行完善,其核心本质是持续改善。
不管是生产设备现场、生产现场、现场管理,企业员工和管理层都能积极参与进去,发现问题的时候通过【CI合理化建议】去提建议,包括流程优化、现场改善等等,共同帮助企业提升效率。

建议表单的填写也十分方便,可以直接通过点击链接、或者扫描二维码的方式,随时随地都能填写,确保发现问题能够及时反馈。
所有的建议都会自动同步到管理层的【员工管理】模块,展示员工好行为、已处理建议、待处理建议等。企业也可以采用积分制,鼓励员工提建议。
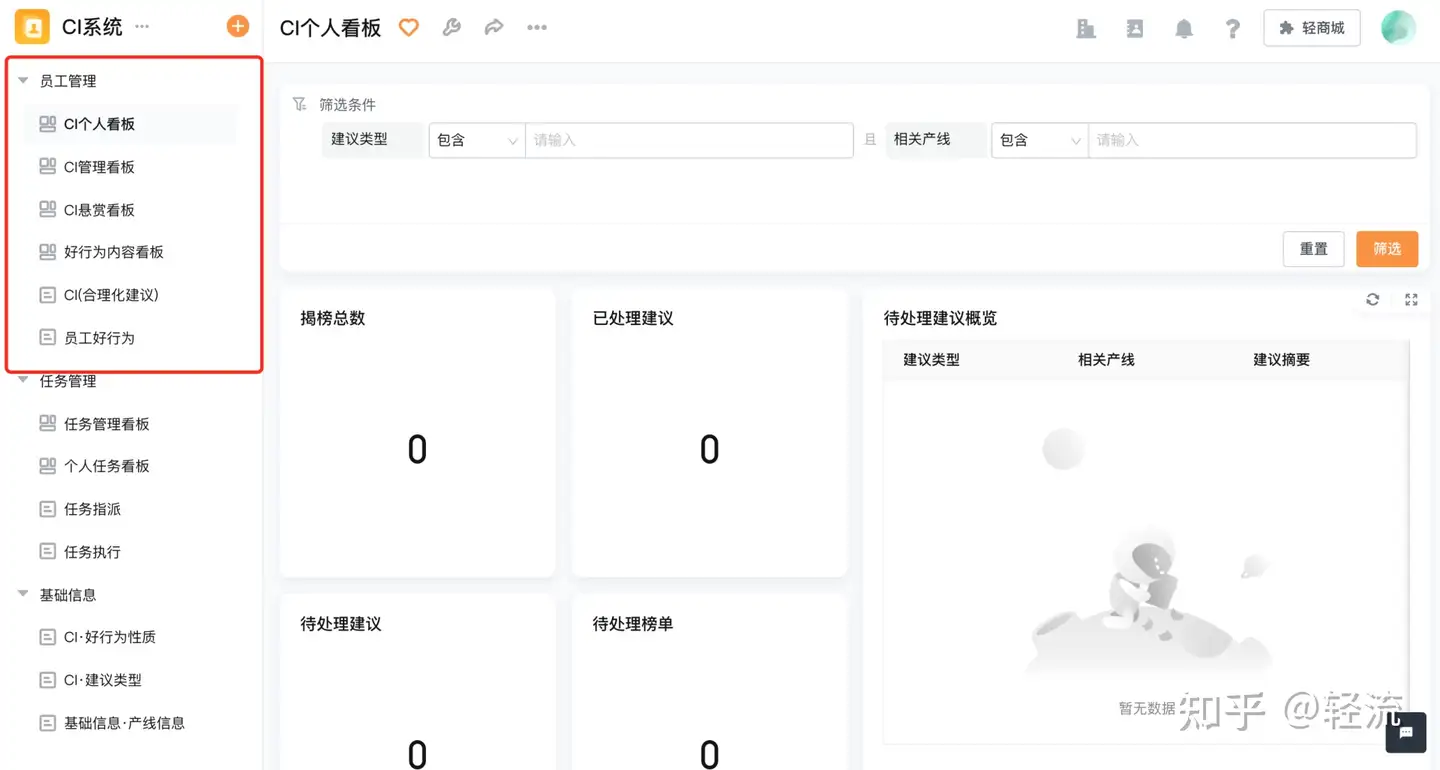
2、QMS质量管理系统
质量管理对于制造业企业来说相当重要,维护产品口碑,维护销量,是否能持续让产品在市场站稳脚跟都与质量管理直接相关。
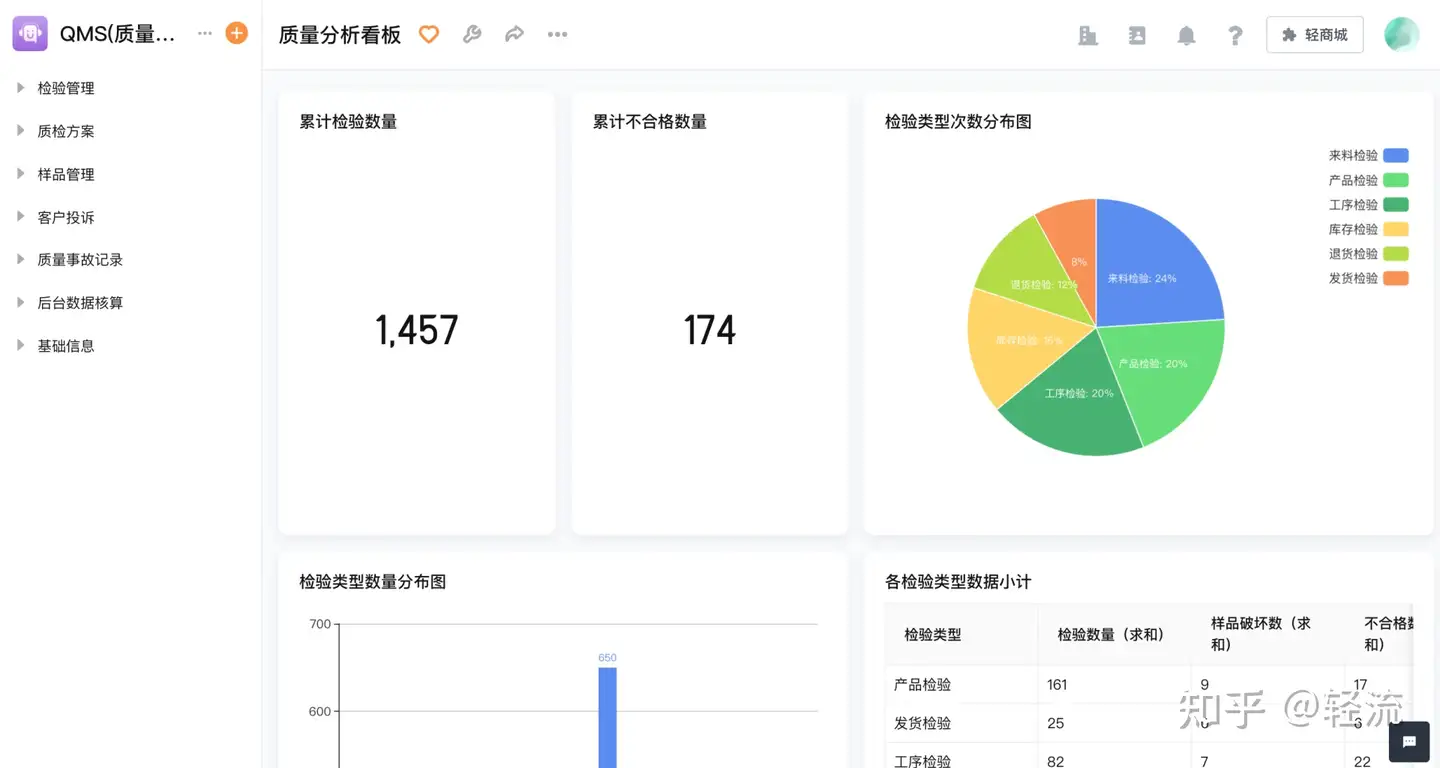
轻流将质量管理划分为四大板块:检验管理(质量管理)、质检方案、样品管理、质量事故记录。通过这四大板块的管理持续改善生产工序、监督生产质量。

【检验管理】中所有类型的检验单、处理单都可以通过分享链接或扫描二维码的形式直接让员工在手机端、电脑端直接填写,操作方便。
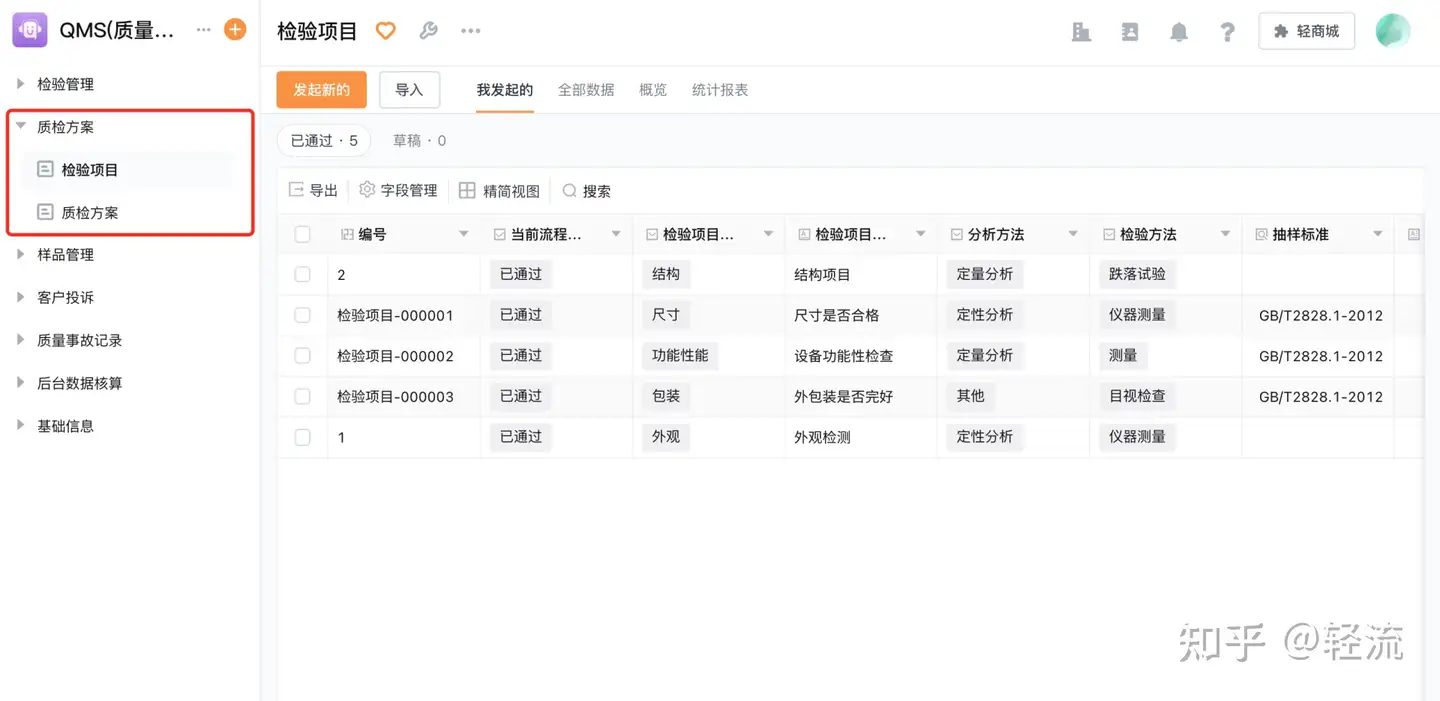
对于重要的检验项目可以制定【质检方案】,创建完成的检验项目会自动流转给检验员,检验员使用规定的分析方法、检验方法进行检验。
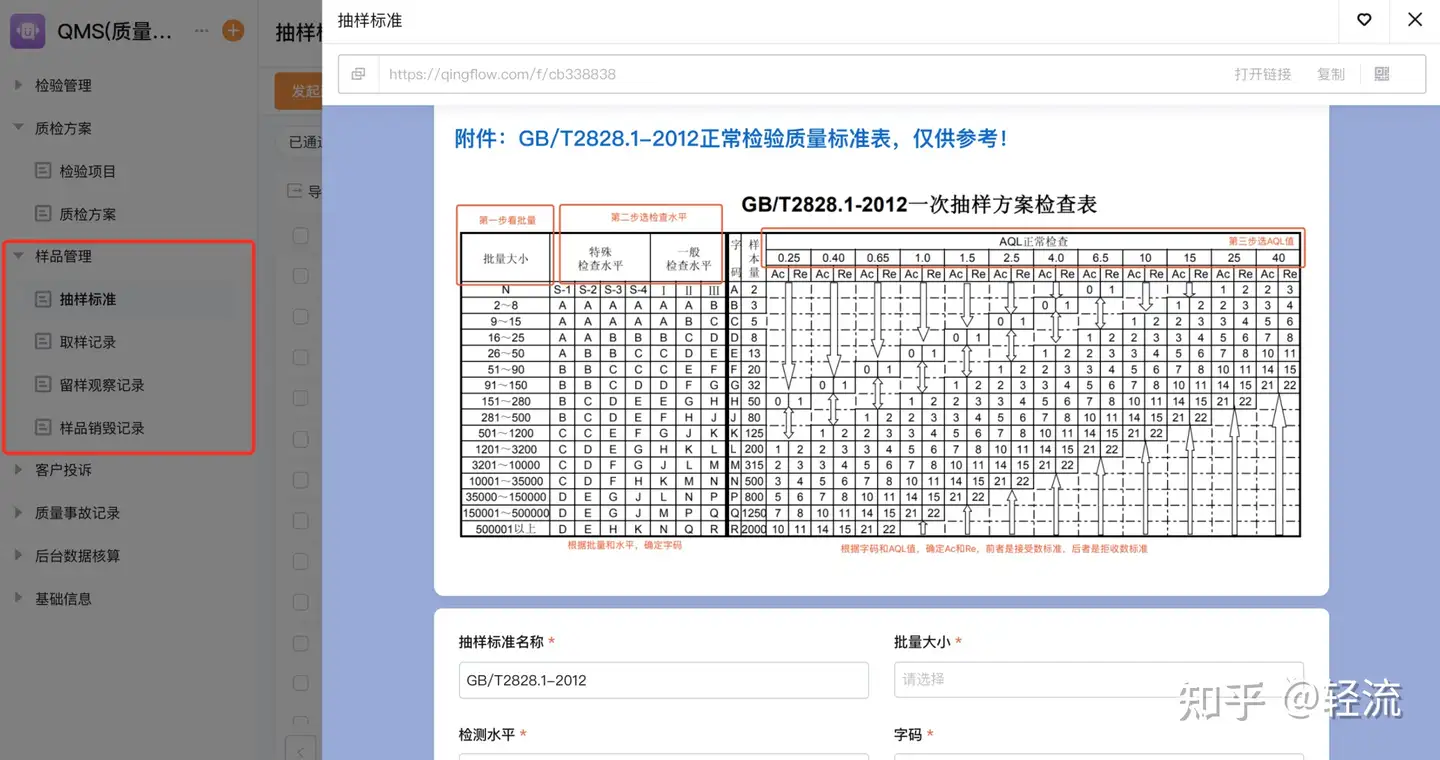
【样品管理】涉及抽样标准、取样记录、留样观察记录、样品销毁记录四个方面,在抽样标准创建表单中提供了GB/T2828.1-2012正常检验质量标准表,以供参考。
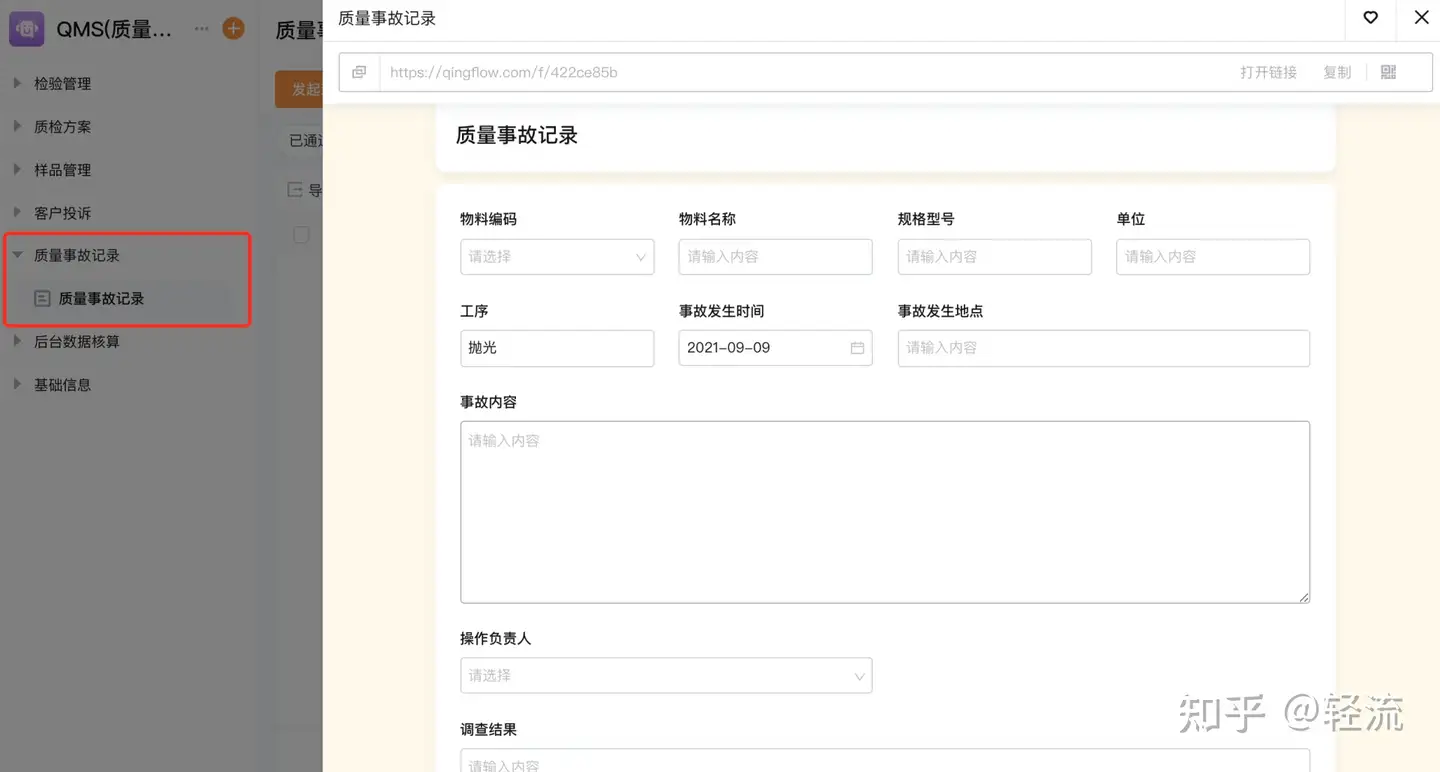
【质量事故记录】可以帮助记录统计质量事故。QMS质量管理系统中检验管理(质量管理)、质检方案、样品管理、质量事故记录模块都是为了精益生产方式中保障质量管理的核心内容,客户投诉、后台数据核算以及基础信息部分可以根据企业实际情况制定自己的质量内容管理板块。
3、健康安全环境管理系统
安全管理也是精益生产管理不可或缺的一部分,通过隐患排查、安全检查、以及基础信息记录能够及时发现存在的隐患,以免造成损失。
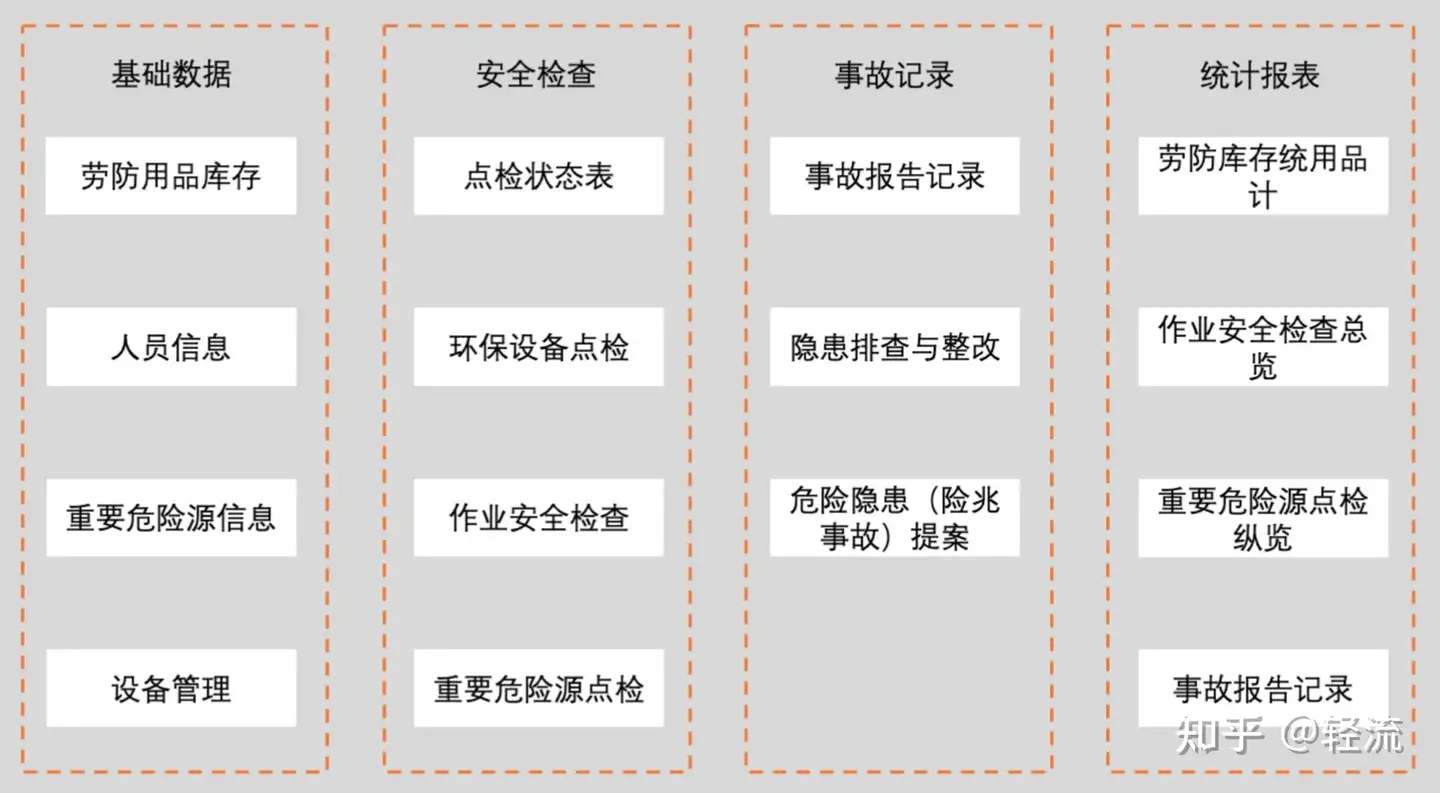
健康安全环境管理系统内覆盖了基础数据、安全检查、事故记录、统计报表四方面内容,将检查和信息相关联,减少重复的工作,有效提升效率。
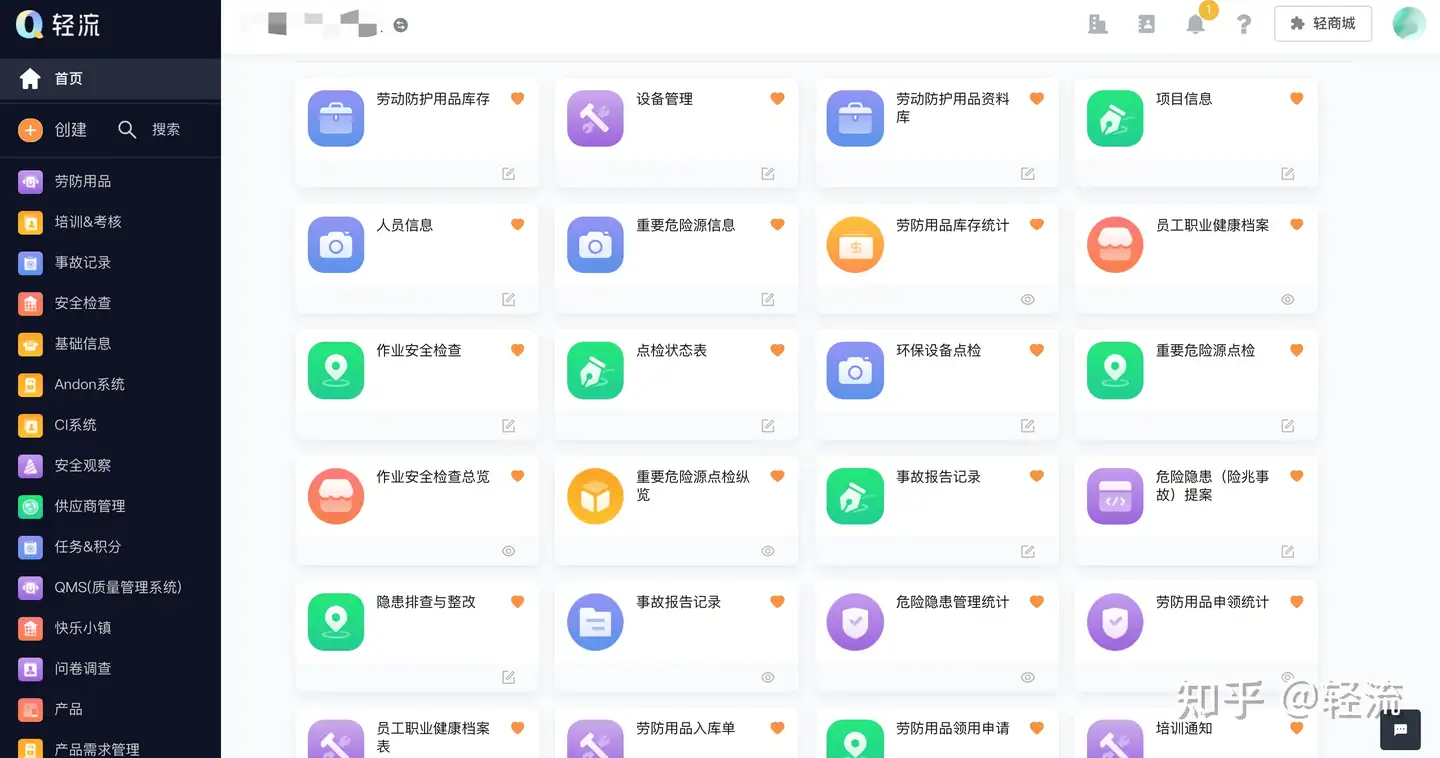
同时,系统内附带了劳保用品的领用和申请,以及相关内容的培训及考试环节,从源头上规范流程,加强员工安全意识,避免事故发生。
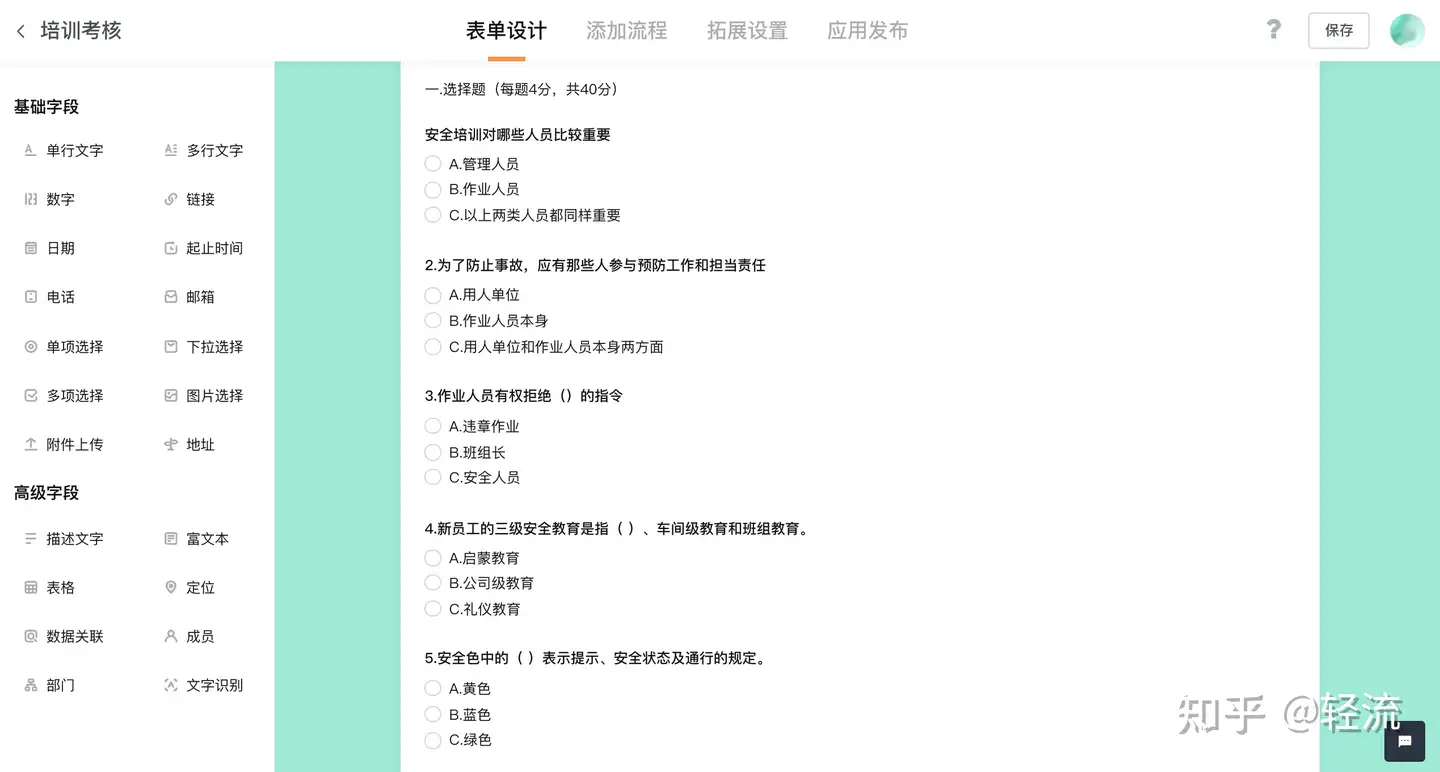
国内大部分制造业企业都面临无法快速响应市场需求、任务下发低效出错、采购生产协同效率低、产能利用效率不高、次品率波动大、优化举措缺乏有效追踪等等问题。
精益生产的管理方式能够解决其中大部分问题。轻流精益制造管理数字化解决方案通过无代码系统,使用信息化手段,从接收客户订单起,到进一步的需求分类、库存变量管理、出库质检流程与核验等流程,井井有条地安排整个业务流程。相比传统的ERP,覆盖的业务范围更广,从核心的生产管理到公司的精益管理,都可以通过轻流 · 无代码系统搭建平台解决。
点击轻流,即可获得精益制造管理数字化解决方案
如果这篇文章对你有用的话,欢迎点赞分享评论~